Medforfattere: Knut Richard Kviserud (OM BE Plast)
Produktutviklerne har nå grunnlag for å velge den beste metoden, basert på tekniske krav, pris og CO2-avtrykk.
3D-printede forminnsatser for sprøytestøping av prototyper og små serier
I prosjektet Rapid Tooling 4.0, ledet av OM BE Plast og støttet av Norges forskningsråd, har vi sett på hvordan vi kan redusere kostnader og tidsbruk i forbindelse med sprøytestøpte prototyper i plast. Metodene er også egnet for små produktserier.
Hovedtemaet i prosjektet har vært innovativ bruk av såkalte forminnsatser (den hvite delen i bildet nedenfor) som er rimelige og som kan fremstilles raskt. Vi har fokusert på forminnsatser lagd med additiv tilvirkning (‘3D-printing’) i egnede polymerbaserte materialer. (Vi sprøytestøper altså ‘plast i plast’). Merk at slike forminnsatser også kan brukes til andre bearbeidingsmetoder for plast og kompositter, f.eks. til formblåsing av brusflasker som nylig demonstrert av Pepsi.
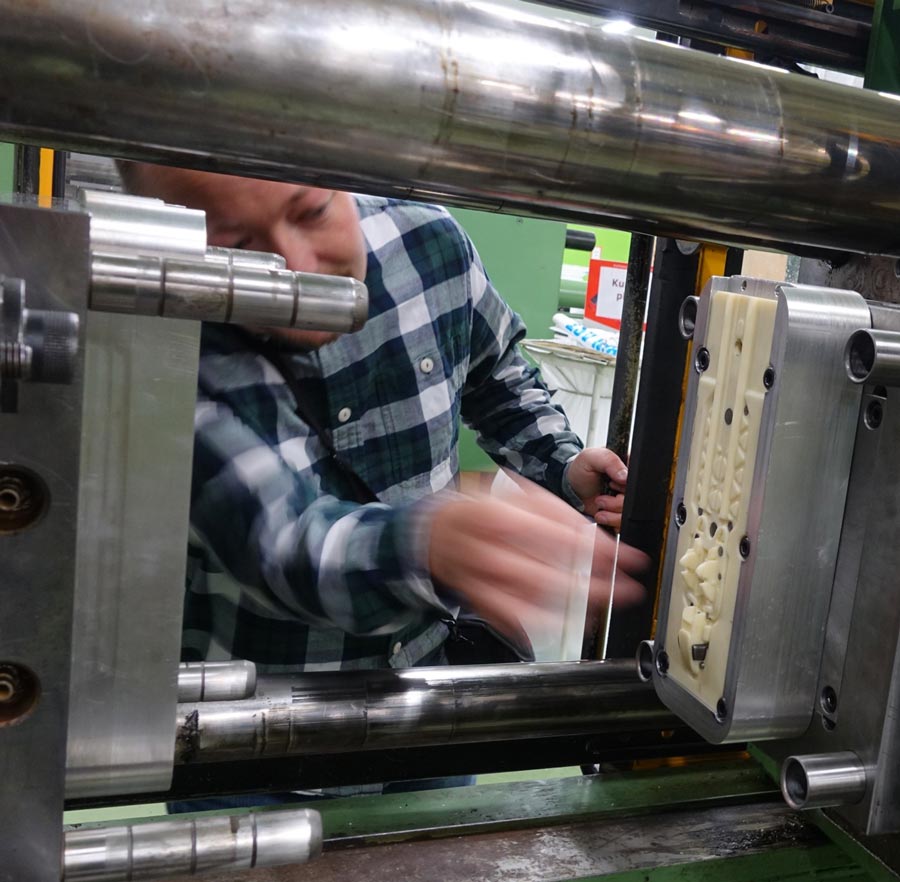
CO2-avtrykket til forminnsatser i plast og metall
I tillegg til utviklingstid og kostnader har industrien stadig mer fokus på bærekraft. Vi ønsket derfor å sammenlikne ulike typer forminnsatser med tanke på bærekraft, nærmere bestemt CO2-avtrykk. Vi har funnet at 3D-printede forminnsatser i visse polymerbaserte materialer har klart lavest CO2-avtrykk. samtidig som de har lav pris og kan framstilles raskt.
Dermed kan slike forminnsatser også bidra til sluttprodukter med bedre bærekraft, da de gjør det mulig å prøve ut en rekke ulike design og materialer, og utføre funksjonelle tester med sprøytestøpte prototyper, enten det er skibindinger, innkapsling av elektronikk eller ventiler til vanndistribusjon. Produktutvikling med bruk av slike forminnsatser kan dermed gi oss produkter med redusert materialforbruk, lang levetid og et materialvalg som er så bærekraftig som mulig – f. eks. gjenvunnet materiale.
Hva bidrar til CO2-avtrykket til en forminnsats?
CO2-avtrykket har bidrag fra produksjonen av råmaterialet (f.eks. en blokk aluminium) og fra produksjonen av forminnsatsen (f.eks. maskinering i aluminium), samt transportkostnader. Svinn fra produksjonen er også tatt med. Energien som brukes i produksjonsprosessene, f.eks. om den er fra kullkraft eller vannkraft, har selvfølgelig innvirkning på CO2-avtrykket. I tillegg til bidragene nevnt ovenfor har vi også vurdert hva som skjer med forminnsatsene etter bruk, f.eks. muligheter for materialgjenvinning, men dette er så langt ikke tatt med i beregnede CO2-ekvivalenter.
Noen forminnsats-alternativer vi har sett på
Vi har tatt utgangspunkt i et konkret formverktøy som vist i nedenfor. Dette har utskiftbare forminnsatser. Vi har bl.a. sett på følgende alternativer:
- Forminnsats 3D-printet i et resinbasert plastmateriale forsterket med glasspartikler: Dette gir en forminnsats som egner seg godt for sprøytestøping, det vil si god overflatefinish (rett fra printeren), høy stivhet og styrke, og høy temperaturresistens.
- Forminnsats 3D-printet i et pulverbasert plastmateriale som inneholder 50 vektprosent aluminiumspulver: Dette alternativet er rimeligere enn alternativ 1 og materialet er robust mot oppsprekking, men overflatefinishen er dårligere og materialet er ikke like stivt.
- Forminnsats maskinert i aluminium: En slik innsats tåler mange flere støp enn alternativene ovenfor. 3D-printedede forminnsatser har imidlertid tilstrekkelig levetid for de fleste prototypeserier. Prisforskjellen avhenger av den geometriske kompleksiteten. Jo høyere kompleksitet, jo dyrere er en maskinert forminnsats i forhold til en 3D-printet forminnsats.
- Forminnsats maskinert i stål: En forminnsats maskinert i et verktøystål er det beste alternativet rent sprøytestøpeteknisk. Maskineringen her og for alternativ 2 er en kombinasjon av fresing og gnisterodering. Mange verktøymakere har mer erfaring med stål enn med aluminium, og i noen tilfeller er prisen for en stålinnsats omtrent den samme som for en aluminiuminnsats.
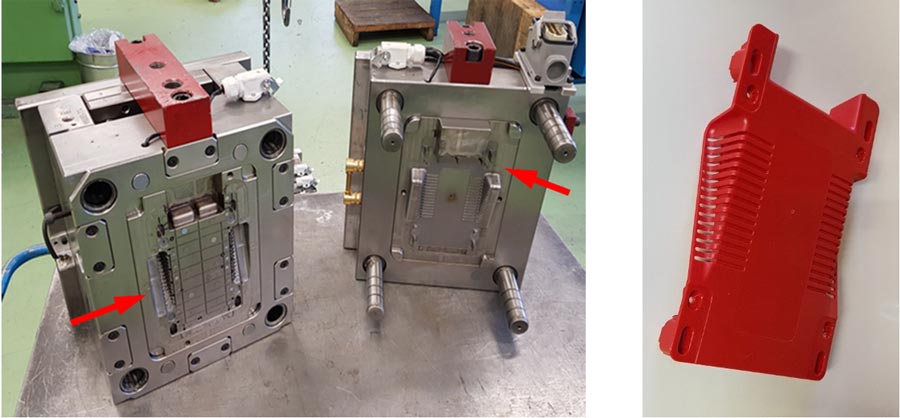
Estimerte CO2-ekvivalenter for utvalgte alternativer
Nedenfor har vi estimert CO2-ekvivalentene for å lage et sett forminnsatser med de fire metodene introdusert ovenfor (med varianter).
- Dette alternativet kommer absolutt best ut med ca 20 kg CO2-ekvivalenter hvis 3D-printet i Norge, og ca 22 kg CO2-ekvivalenter hvis 3D-printet i Belgia og transportert til Norge. (20 kg CO2-ekvivalenter tilsvarer CO2-fotavtrykket til ca 0.9 kg storfekjøtt i butikkhylla eller 75 km med en bensinbil.) Omtrent 85% av CO2-avtrykket til dette settet av forminnsatser skyldes produksjon av råmaterialet, altså den såkalte resinen i dette tilfellet (antatt produsert i Nederland i vårt tilfelle). Materialer med og uten glasspulver som forsterkning kommer ganske likt ut.
- Alternativ 2 gir et mye høyere CO2-avtrykk enn alternativ 1 (ca 6 ganger høyere). Igjen er det råmaterialet (antatt produsert i Tyskland i dette caset) som gir det største bidraget, og CO2-avtrykket er omtrent det samme om printingen gjøres i Norge eller Belgia (med transport til Norge). Råmaterialet i dette alternativet gir et høyt CO2-avtrykk p.g.a. aluminiumspulveret (50 vekt %) og det faktum at akkurat dette materialet (p.g.a. aluminiumspulveret) gir mye svinn da pulver fra byggekammeret ikke kan gjenbrukes i 3D-printeprosessen. I prinsippet kan imidlertid dette pulveret materialgjenvinnes f.eks. i sprøytestøping, så her er det muligheter for å redusere CO2-avtrykket. CO2-avtrykket kan også reduseres ved å printe forminnsatsene med baksiden «åpen» eller med en stiv gitterstruktur. Den åpne baksiden kan eventuelt fylles med en forsterket herdeplast (stivere enn printematerialet) med lavt CO2-avtrykk slik at forminnsatsen får en bedre ytelse (stivhet og styrke).
- Alternativ 3 gir et mye høyere CO2-avtrykk enn alternativ 1; ca 6-7 ganger høyere hvis maskinert i Norge og ca 9-10 ganger høyere hvis maskinert i Europa. Igjen er det råmaterialet som gir det dominerende bidraget til CO2-avtrykket. I begge tilfeller har vi antatt at aluminiumslegeringen er produsert i Europa (ikke Norge). Dette er sannsynlig siden slike spesiallegeringer (for høyhastighetsfresing av forminnsatser) ikke lages i Norge. For forminnsatser til prototyper kan imidlertid norskprodusert aluminium være godt nok, og dette vil redusere CO2-avtrykket. Videre vil bruk av resirkulert aluminium redusere CO2-avtrykket betraktelig. Vi har også sett på en variant der kinesisk-produsert aluminium maskineres i Kina. En slik forminnsats vil ha mer enn 20 ganger høyere CO2-avtrykk enn alternativ 1.
- Alternativ 4 (forminnsatser i stål) er noe bedre eller likt alternativ 3 (forminnsatser i aluminium), avhengig av geografien. For europeisk råmateriale maskinert i Norge gir stål en reduksjon på 20% i CO2-avtrykk sammenliknet med aluminium. Reduksjonen er omtrent den samme for kinesisk råmateriale maskinert i Kina. For europeisk råmateriale maskinert i Europa ser vi ingen forskjell mellom stål og aluminium. Merk at absoluttverdiene for CO2-avtrykket er rangert som for alternativ 3: Europeisk råmateriale maskinert i Norge kommer klart best ut.
Usikkerhet i datagrunnlaget
Beregningene av CO2-avtrykk er utført av Asplan Viak. Det er dels brukt generiske data fra databasen ecoinvent v3.6, og dels mer spesifikke data for 3D-printeprosessene og tilhørende materialer. Det er imidlertid en del usikkerhet i datagrunnlaget. Prosjektpartner SINTEF jobber med å forbedre grunnlaget for slike beregninger, bl.a. for å få mer eksakte livsløpsanalyser for 3D-prining sammenliknet med tradisjonelle bearbeidingsmetoder.
Hva med direkte 3D-printing av prototyper?
Prototyper kan jo også 3D-printes direkte. Dette er blitt den vanligste metoden for å lage prototyper i plast. Per i dag får man imidlertid ikke helt de samme materialegenskapene som ved sprøytestøping, og overflatefinishen er heller ikke like god. Videre er det mange spesialmaterialer for sprøytestøping som ikke er tilgjengelige for 3D-printing, inklusive nye bærekraftige materialer.
Uansett er likevel 3D-printede prototyper godt nok for mange formål. Vi vil komme tilbake til CO2-avtrykket til forskjellige typer plast-3D-printing i en egen blogg, men to faktorer kan nevnes her: 1) Et viktig bidrag til et bærekraftig 3D-print er at selve 3D-printeren utnyttes godt, d.v.s. at den printer så mange (nødvendige!) deler som mulig i sin levetid. 2) De 3D-printede delene bør materialgjenvinnes. Dette er enklest om materialet er en termoplast. Delene kan da f.eks. kvernes opp for å lage nytt filament til 3D-printing (dette kan gjøres av lokale aktører, f.eks. en såkalt ‘makerspace’). Ellers har sprøytestøpebedrifter slike kverner, og oppkvernet materiale kan sprøytestøpes direkte eller blandet med annet materiale (nytt eller gjenvunnet). En bør da holde seg til ett eller få 3D-printematerialer som er anvendelige i sprøytestøpte produkter.
Kommentarer
Ingen kommentarer enda. Vær den første til å kommentere!